2010 Camaro Idler Pulley Ball Bearing Analysis
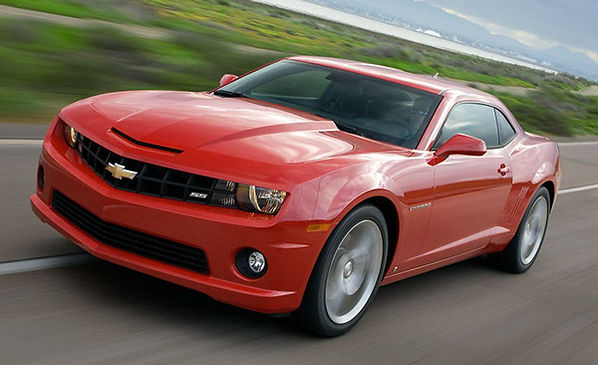
Challenge
How to accurately model stresses and strains of idler pulley bearings
Process
Utilized Solidworks and ANSYS to develop three different models and test for accuracy
Impact
Validated bearing performance, improved technical knowledge of CAD/FEA analyses
Background:
Within the 2010 Chevy Camaro SS’s serpentine belt system, an idler pulley is required to regulate how the belts run from the crankshaft to generate movement in other parts and engine accessories. The idler pulley has a ball bearing within to reduce rotational friction and support radial and axial loads on the pulley. The idler pulley utilizes a single-row, deep-groove ball bearing with a pressed steel cage and a double lip contact rubber seal. The bearing itself is press-fit into the outer "shell", forming the entire pulley assembly. I was tasked with both the CAD modeling of the ball bearing and the FEA simulation of the idler pulley’s in-application stresses.
Design Considerations:
-
The differences in the three models forced me to relatively judge the importance of the various aspects of the models.
-
For instance, I discovered that the contact area of the ball bearing on the simulated raceway had massive implications on the resulting stresses and safety factors.
-
-
The figures below do not just depict discrete results, but they also illustrate a deep-set work ethic that inspires me to continuously improve, even when improvement is not expected or required.
#1 - Initial, Exploratory CAD/FEA Model
#2 - Refined, Oval-shaped Contact Model
#3 - Final, Full CAD/FEA Model

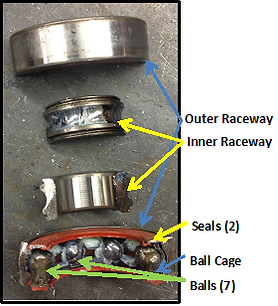



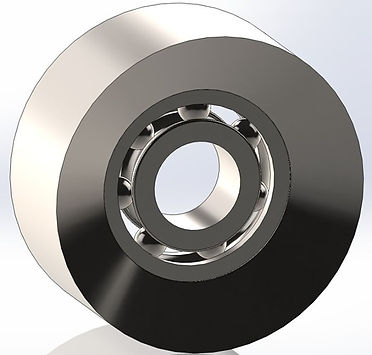
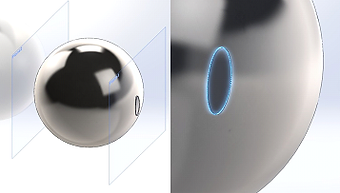
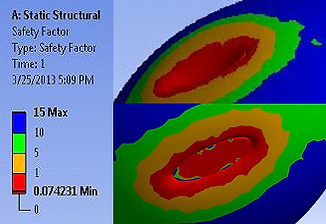

